SafeDE News
Smarter workplaces are safer workplaces. SafeDE is your resource for OSHA news, regulation changes, recalls, and everything to keep your business safe.
Comprehensive Guide: Identify Workplace Hazards (5 Steps)
A hazard refers to any condition or circumstance in the workplace that can potentially cause damage, harm, or adverse health effects to individuals or property under specific conditions. The Occupational Safety Hazard Administration (OSHA) emphasizes that every workplace must be prepared to identify potential hazards to reduce the risk of injuries or fatalities before they even occur.
5-Step Guide to Identify Workplace Hazards
Hazard identification consists of five major courses of action based on OSHA recommendations and policies:
- Gather existing data on workplace hazards
- Conduct a workplace inspection for safety hazards
- Report all health-related hazards
- Perform incident investigations
- Recognize the hazards linked with emergency scenarios
Each step will be discussed in detail below.
Gather Existing Data on Workplace Hazards
Employers and workers must provide all the available information related to their workplace to identify existing hazards. Here are examples of internal and external sources of relevant data:
- User manuals for operating machinery and equipment
- Official Safety Data Sheets (SDS) from chemical manufacturers
- Outcome reports of job safety analyses (JSAs) or job hazard analyses (JHAs)
- Internal inspection reports on exposure monitoring, maintenance, and safety, including worker incident logs and redacted medical records
- External inspection reports from insurance providers, consultant groups, and government agencies
- Employee compensation records and any associated reports
- Existing safety and health protocols regarding confined spaces, personal protective equipment (PPE), lockout/tagout, and process safety management
- Employee input during safety & health committee meetings and feedback from surveys
- Official alerts and publications from OSHA, Centers for Disease Control and Prevention (CDC), and the National Institute for Occupational Safety and Health (NIOSH)
- Information provided by labor unions, trade associations, worker advocacy organizations, and local occupational safety and health coalition groups
Conduct a Workplace Inspection For Safety Hazards
Hazards that did not exist before may emerge gradually due to equipment wearing down, worksite degradation, or maintenance lapses. Regular workplace inspections should be performed to proactively eliminate hazards before they become major concerns.
Here are some examples of conducting an effective workplace analysis or inspection:
- Encourage employees to collaborate with inspection teams and encourage them to report any hazards they observe.
- Document inspections meticulously to track corrective actions taken. Record videos and take photos of areas that are likely the become future areas of concern.
- Conduct thorough inspections of all workplace areas and on-site activities. These include but are not limited to storage, maintenance, office functions, and contractor activities.
- Perform regular inspections for every vehicle used in the workplace, from forklifts to transport trucks.
- Utilize checklists that highlight workplace-specific hazards that are divided into relevant categories.
- Inform employees before implementing changes in work operations, equipment, and materials and ask for their feedback on these changes.
Most workplace safety hazards are identifiable using simple observation and common sense. Additionally, OSHA has an online Hazard Identification Tool that provides interactive, game-based training on the fundamentals of recognizing safety hazards. Proper training of workers on hazard identification and risk assessment will improve their efficiency in tracking and reporting sources of danger on-site.
Report All Health-Related Hazards
Health hazards include any substance or object that poses a danger to human life and can be ergonomic, chemical, physical, or biological. These can be more challenging to identify than safety hazards because they often do not have obvious signs, or their harmful effects appear much later.
- Ergonomic risk factors are distinguished by evaluating and monitoring tasks that involve repetitive motions, significant vibration, heavy lifting, or overhead work.
- Physical hazards most likely exist in places with excessive noise from heavy machinery or tools, radioactive materials, or elevated temperatures.
- Biological hazards include illnesses caused by exposure of workers to molds, poisonous or toxic wildlife, or infectious diseases. Skin allergies or occupational asthma triggered by animal hair or droppings should also be recorded.
- Chemical hazards can be pinpointed by reading product labels and Safety Data Sheets (SDS). Keep an eye out for chemicals with high volatility, have low exposure limits, or are used extensively in areas with poor ventilation. On-site activities where skin exposure to chemicals is frequent should be monitored as well.
- Perform quantitative exposure assessments using direct reading or air sampling instruments to obtain accurate readings of exposure levels that may cause illness.
- Review employee medical records for any impairments, conditions, or diseases possibly linked to workplace exposures. Make sure to redact any information that protects employee privacy when accessing their medical records.
Perform Incident Investigations
Workplace incidents—whether near misses, illnesses, or non-fatal accidents—are pivotal indicators of existing hazards. Building a proper system to investigate these incidents is important in ensuring that they are less likely to happen again.
- Create an incident investigation plan with a clear outline, objectives, and procedures. Set up the necessary communication channels, equipment, and reporting templates to ensure that the plan can be activated immediately when required.
- Invest in training the investigative team members with the appropriate skills and techniques that emphasize open-mindedness, objectivity, and efficiency.
- Investigation teams should include representatives from the workforce and the management. Encourage them to participate during worksite inspections or incident investigations so that everyone becomes competent in hazard identification procedures.
- Do not disregard near-miss or close-call incidents. These should also be investigated properly so that they would be less likely to re-occur as serious accidents in the future.
- Trace any workplace accidents back to their root source so that intervention programs or policy changes can be implemented to eliminate their reoccurrence.
- Share the findings of all workplace investigation reports with the management and employees to raise awareness and help them avoid potential sources of hazards.
An effective incident investigation does not stop at locating the source of an accident. If a piece of equipment stops working, the investigation team should ask questions about why it failed, what led to its failure, how was it maintained, and how it can be prevented again. The probing should not stop there; even if it was concluded that an employee caused the error, investigate if that worker was given the right tools and time to complete the work or if they were supervised correctly during the operation.
Recognize the Hazards Linked with Emergency Scenarios
Emergencies are non-routine events that bring forth unforeseen hazards that may cause severe damage unless they are identified quickly. Here are examples of such situations:
- Structural collapse
- Fires and explosions
- Release or spillage of chemicals or hazardous materials
- Electric shortages
- Non-routine maintenance operations
- Equipment restarts after planned or unplanned shutdowns
- Flooding
- Structural collapse
- Outbreak of disease
- On-site medical emergencies
- Workplace violence
- Weather and other natural disasters
Anticipating foreseeable situations requires planning and consideration of factors such as the workplace facility layout, equipment maintenance, materials storage, and overall preparedness of the management and its employees.
Frequently Asked Questions (FAQs)
What is hazard identification and why is it important?
Hazard identification is the comprehensive process of evaluating if a specific location, object, or substance has the potential to endanger the workers, supervisors, and their managers. It is important in reducing the incidence of work-related injuries and fatalities.
What are the 5 steps to identify workplace hazards?
The first order of action is to gather existing information on workplace hazards from internal and external sources. Once the data is compiled and evaluated, the next steps are to identify any workplace-related and health-related hazards and to organize incident investigation teams. All incidents and emergencies that occur in the workplace must be investigated in depth to prepare the employees, supervisors, and managers for unforeseen hazards.
How do you recognize and control workplace hazards?
Workplace hazards are recognized by conducting on-site inspections and analyses of all occupational areas, activities, vehicles, and equipment. During these inspections, the management and employees must cooperate in identifying all sources of potential harm. Employee feedback should also be collected during the implementation of operational changes and new equipment to prepare everyone for unforeseen incidents.
What are some hazard identification methods?
Hazards can be proactively avoided by reviewing operations manuals, safety data sheets, employee compensation records, incident reports, and public information on hazards. Workplace inspections are also conducted to evaluate the condition of equipment, vehicles, and materials and ensure that they do not cause any injury or illness to people working on-site.
How can a worksite analysis help identify hazards?
A worksite analysis is an organized process of hazard identification by reviewing workplace-specific operations, areas, and policies that are the most likely sources of accidents and injuries.
What is the OSHA hazard identification training tool and how can it be used?
The OSHA Hazard Identification Tool was developed to help train small business owners and their employees on the basics of workplace hazard recognition. It can be downloaded for free from OSHA’s official website as a fully interactive, game-based version or a full-text version.
Get SafeDE News
Workplace safety for all businesses.
SafeDE provides FREE comprehensive onsite surveys for small and medium sized private sector establishments to identify potential workplace hazards, improve safety and health management systems, and assist in voluntary compliance with federal OSHA regulations.
Related News
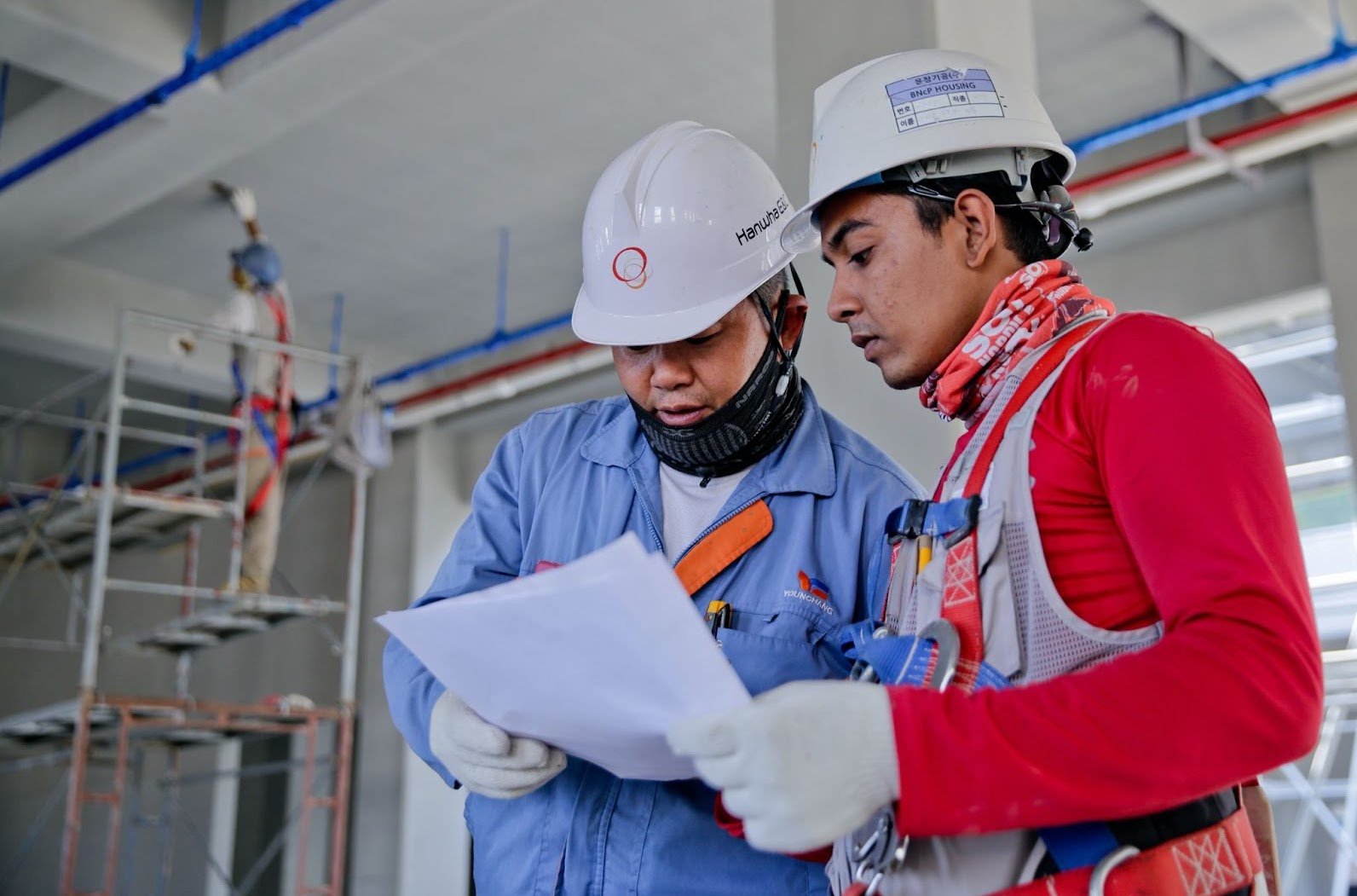
Understanding DART Rate: Calculation, Formula & Meaning
-1.png)
Recognizing Warning Signs of Heat Illness at Work
-1.png)
Crane Hand Signals: Guide to OSHA-Compliant Safety
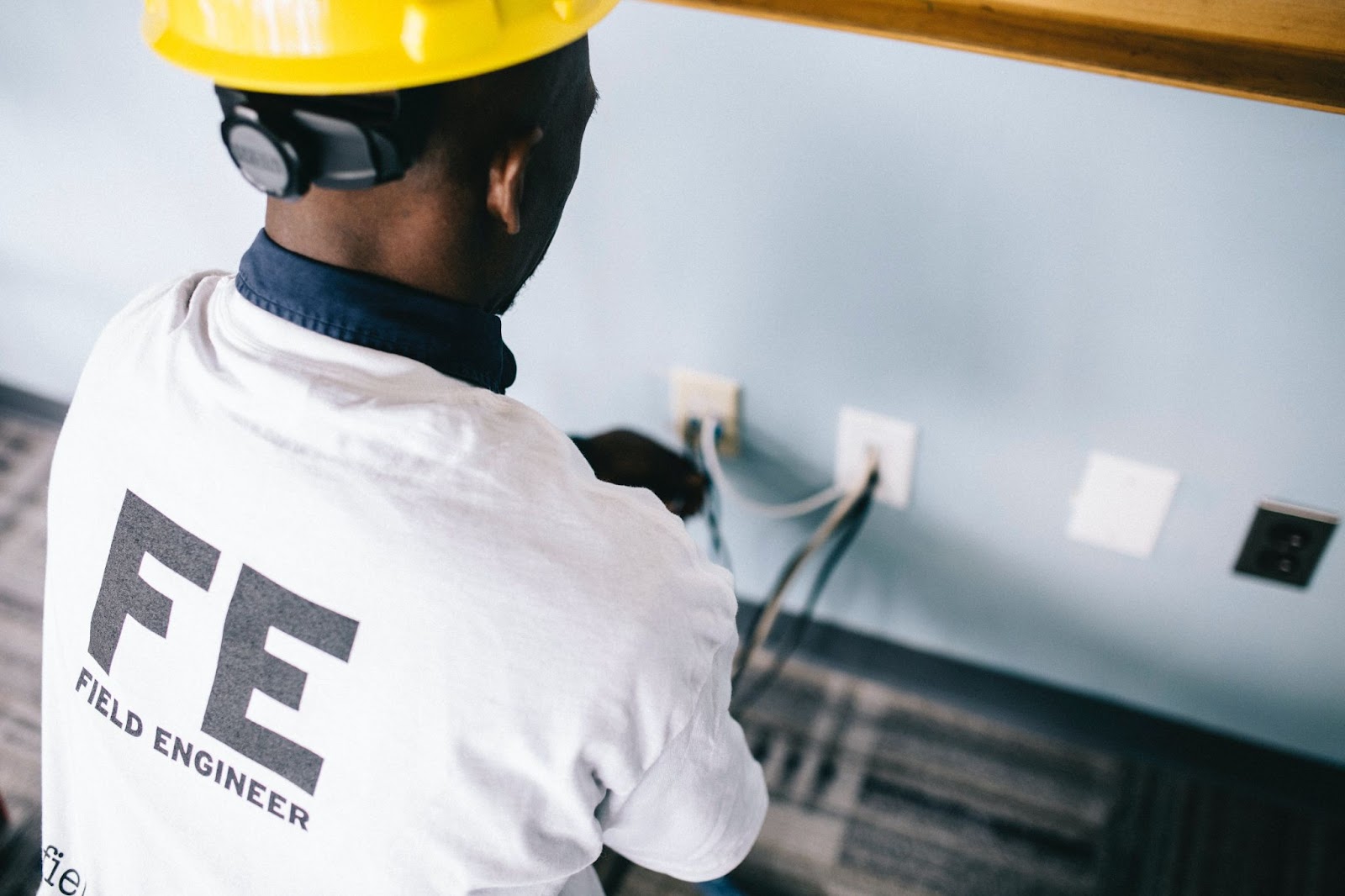
Preventing Arc Flash Injuries: Safety Tips & Prevention
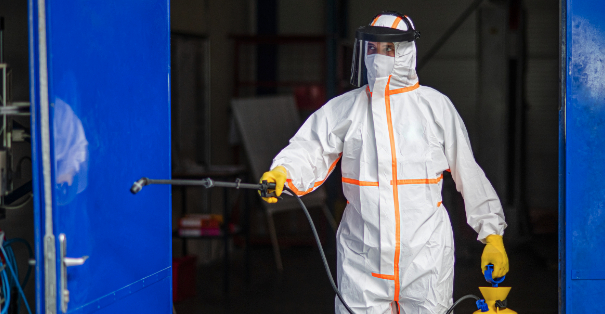
Essential PPE for Staying Safe and Comfortable in Hot Work Environments
.png)
GHS Label Requirements for Shipping: Tips and Guidelines
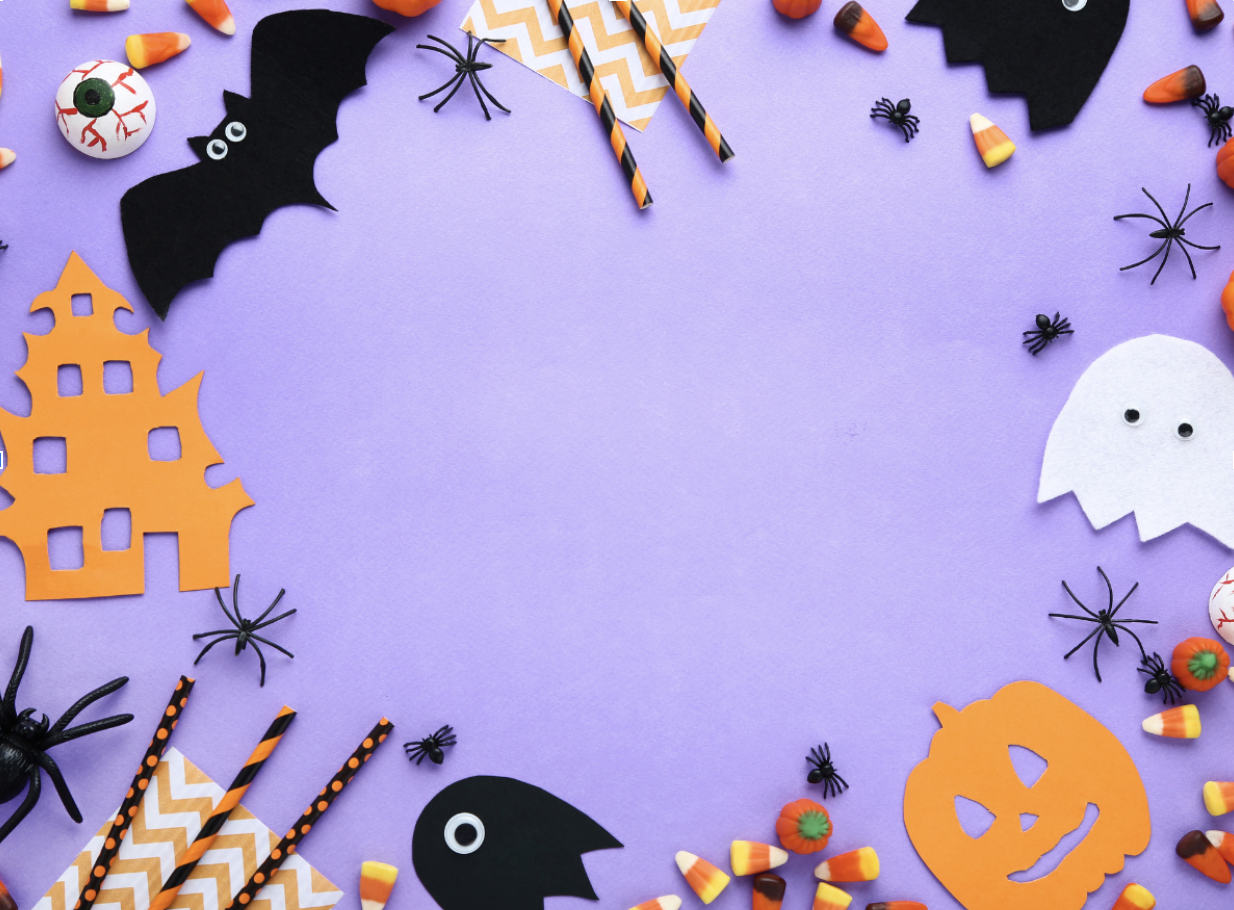
Your Complete Guide to Workplace Health and Safety During Halloween
-1.png)
Back Safety Tips: Prevent Injuries in the Workplace
-1.png)